Waste to Bio-ethanol (WTBe) technology utilizes Agricultural waste and Municipal Solid Wastes (MSW) to create bioethanol and bio-product through various complex conversion methods.
This technology provides an alternative source of renewable energy in a world with limited or challenged remnant reserves and there is a significant excess supply of MSW (primarily in landfills) around West Africa.
The demand for MSW as a bioethanol source has increased, driven by the rising costs of landfill disposal and difficulties in expanding existing landfill capacities.
Ecogreen 5link has provides an overview of the primary methods of transforming agricultural waste to energy via the processes of distillation, plant processes, and EfW processing.
The distillation technology employed in producing bioethanol has been well proven in the world over 100 years ago.
Plants are available in three standard sizes: –
Plants processing up to 50,000 or 90,000 tonnes of waste per year are supplied with one EfW processing chamber including semi-automatic sorting. A plant processing up to 200,000 tonnes of waste per year is supplied with two EfW processing chambers and includes fully automatic sorting equipment.
The resultant sanitized biomass is used as the ‘feedstock’ to be distilled into high yield bioethanol
Lignin, a by-product of the process, is formed into briquettes to fuel the steam boilers that run the plant Solar panels are included in the structure of the roof to generate electricity and insure a totally green technology Metals and plastics are recycled and sold for extra revenue The patented EfW processors are neither sealed nor pressurized, this safety design element is specifically incorporated in order to eliminate any risk of high-pressure explosions.
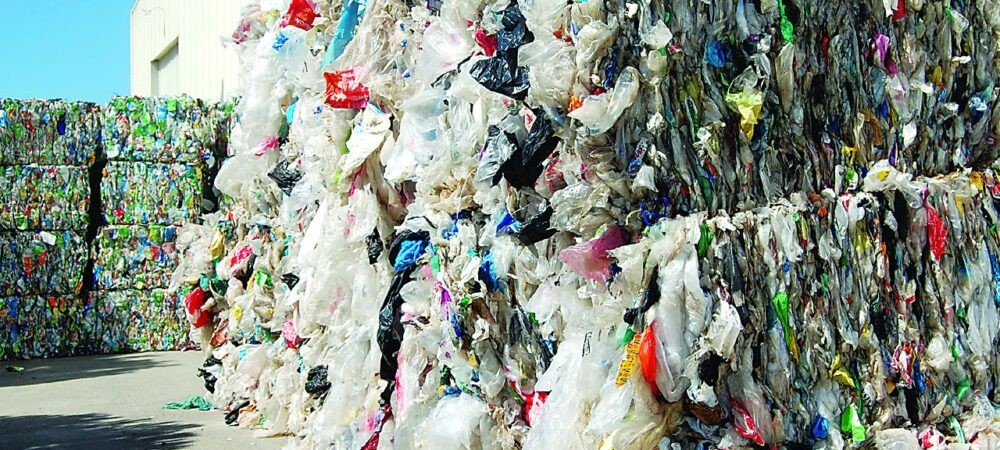
Ecogreen 5link in partnership with Energy from Waste Ltd has developed a revolutionary green technology that converts municipal and agricultural waste into bio-ethanol, in a continuous, non-stop, flow process.
Superheated steam is injected into a double, contra-rotating, open-ended, non-pressurized chamber to open up the fibers of the waste making it suitable for conversion into a high yield bioethanol.
A large plant can take up to 200,000 tonnes of household or agricultural waste per year and convert it into 36 million litres of bio-ethanol.
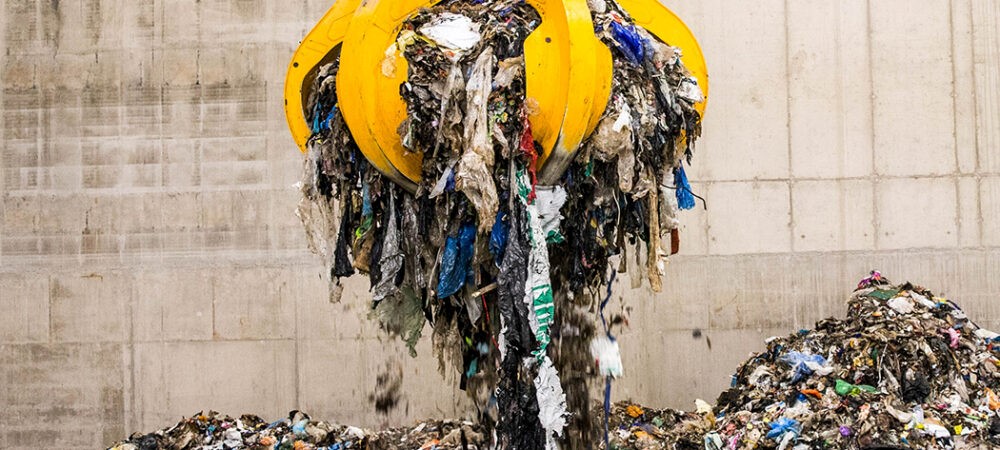
SCHEMATIC – WASTE TO BIOETHANOL PROCESSING PLANT
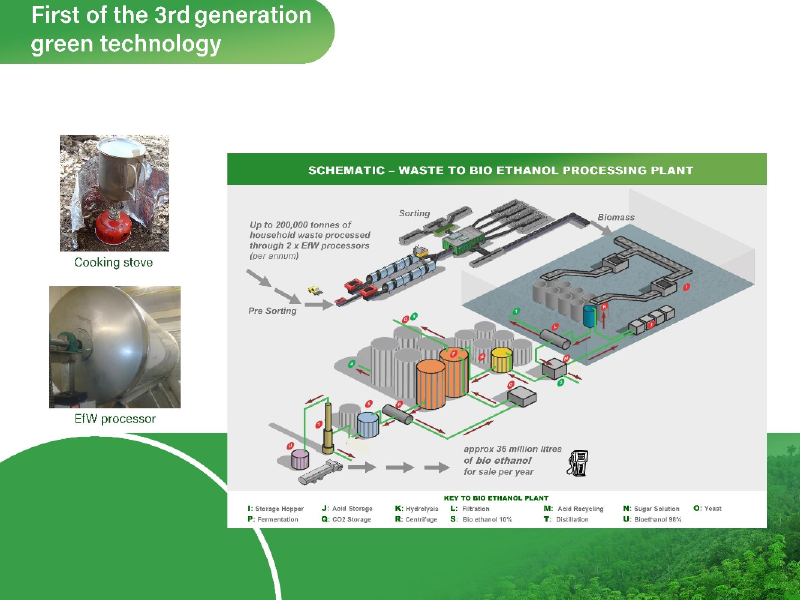
Summary
- A fraction of the cost of a comparable incinerator plant – much lower running costs from new proven technology
- A continuous non-stop process that ensures production is infinitely faster and easily expandable
- The overall volume of waste substantially reduced following processing
- Resultant product and residue of bio-mass is sanitized ready for processing
- No toxins or odours to atmosphere patented odour control system
- A considerable number of new jobs created with each project
Incorporated in the ductwork that serves the EFW waste processor is an odour control system that is capable of neutralizing any unpleasant smells resulting from the process.
By combining ultraviolet light with titanium, we create ozone, we then convert the ozone back to oxygen, this process ensures that offensive odours are eliminated from the process and that any airborne compounds are greatly reduced.
The odour control unit comprises two separate chambers each containing UV lamps producing ultraviolet light at different frequencies.
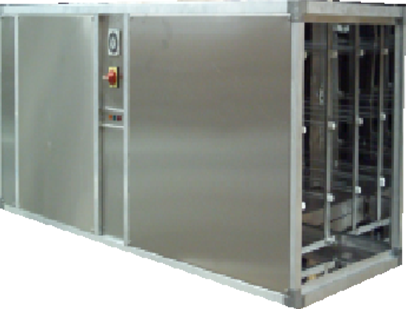
Air enters the first chamber and passes through a series of blades that turbulent the air whilst exposing it to ultraviolet light at 184nm. As the odour is removed much of the ozone and hydroxyl radicals are consumed.
Any ‘carry-over ‘of ozone is then passed through to the second chamber where it is exposed to ultraviolet radiation at 254nm. This has the effect of breaking down the ozone into single oxygen atoms reverting it back to oxygen
Once the above process has been completed, any air expelled from the EFW waste processor can be safely discharged into the atmosphere
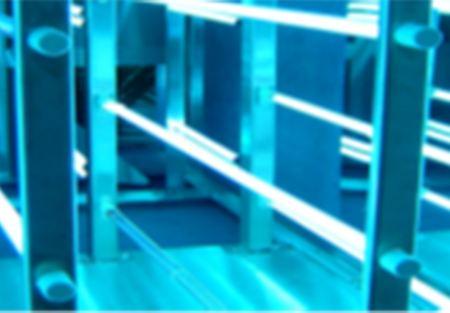